Aluminum Hydraulic Cylinders
HDM is a leading manufacturer of aluminum hydraulic cylinders. These aluminum cylinders are durable, lightweight, and typically used in highly corrosive environments. Our aluminum hydraulic cylinders are rated to accommodate up to 3,000 PSI operating pressures.
Whether your application requires a single acting or double acting cylinder, we have the engineering and manufacturing expertise to help you obtain the precision aluminum cylinders that meet your high standards.
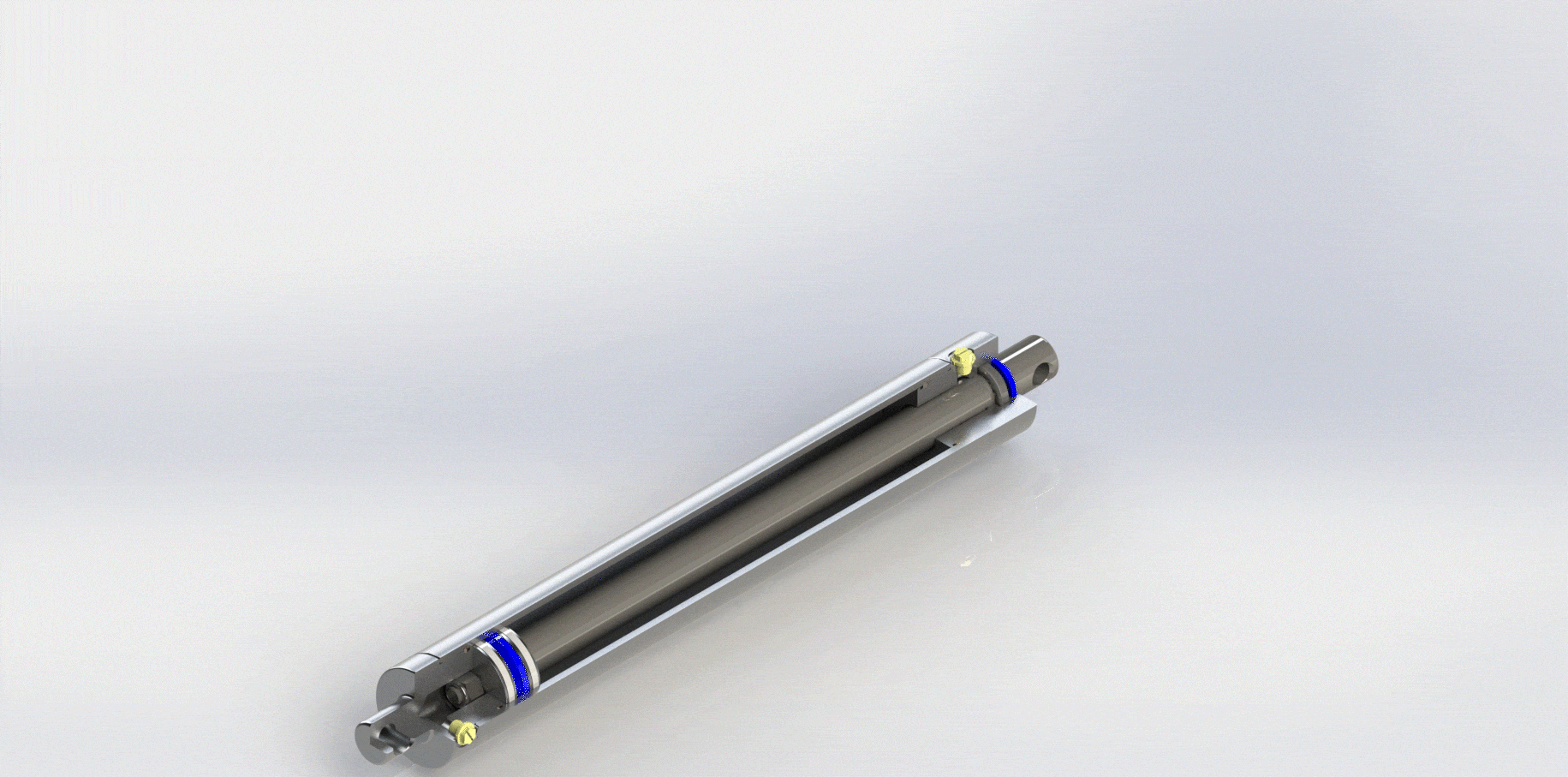
The cylinder consists of a piston inside a sealed barrel, which moves back and forth as pressurized hydraulic fluid is introduced to either side of the piston. This movement can produce significant force, enabling the cylinder to push, pull, or lift loads.
Our aluminum hydraulic cylinders are ideal for applications where weight reduction is crucial, such as in mobile equipment or aerospace, without sacrificing strength or performance. They are also highly resistant to corrosion, making them suitable for use in environments that expose the cylinder to moisture or chemicals. We treat our aluminum with a variety of processes to prevent oxidation and protect the underlying material from moisture, chemicals, and other corrosive substances.
Markets include:
- Agriculture
- Automotive
- Aviation
- Construction
- General Industry
- Metalworking
- Mining Quarrying
Applications include:
- Clamping
- Lifting
- Material Handling
- Packaging
- Position Sensing
- Punching
- Steering

Smooth Operation

Light Weight

Anodized Treated

Corrosion Resistant
General Features & Specifications
Our aluminum hydraulic cylinders are rated to accommodate up to 3,000 PSI operating pressures. They have numerous features that make them useful in a range of applications, including:
• Lightweight. Their low density makes them significantly lighter than steel and easier to handle, install, and transport. This characteristic is especially beneficial in applications with precise weight restrictions such as aerospace, automotive, and mobile equipment.
• Corrosion Resistant. Because aluminum naturally forms an oxide layer, the material is protected from rust and corrosion, making aluminum cylinders ideal for use in corrosive environments such as chemical and marine.
• Superior Thermal Conductivity. Aluminum’s excellent heat dissipation properties can help reduce the risk of hydraulic systems overheating when they operate at high temperatures.
• Cost Efficiency. Although steel can be less expensive in raw form, aluminum's corrosion resistance and lower maintenance costs can result in long-term savings in specialized or small-scale applications.
• Material Strength. Aluminum is a strong material, but not as strong as steel. As a result of this reality, aluminum hydraulic cylinders are typically used in low- to medium-pressure applications and are not suitable for high-pressure environments, where steel cylinders are more common.
• Fatigue Rate. Compared to steel, aluminum cylinders have lower fatigue resistance, so they may not last as long in applications with repetitive or cyclic loading unless designed with this in mind.
In summary, aluminum hydraulic cylinders are ideal for applications where weight savings, corrosion resistance, and heat dissipation are priorities and are best suited to low- to medium-pressure applications.
Custom Aluminum Hydraulic Cylinders
Aluminum cylinders are highly customizable. Because aluminum is easier to machine than steel, it is easy to customize an aluminum cylinder's dimensions, fittings, or connections. This feature of the material allows for more flexibility in design, especially in low- to medium-pressure applications.
The features we can customize include:
- Bore Size
- Caps
- Heads
- Mounting Style
- Pistons
- Rods
- Rod Seals
- Stroke Length
- Tubes
- Tube Seals
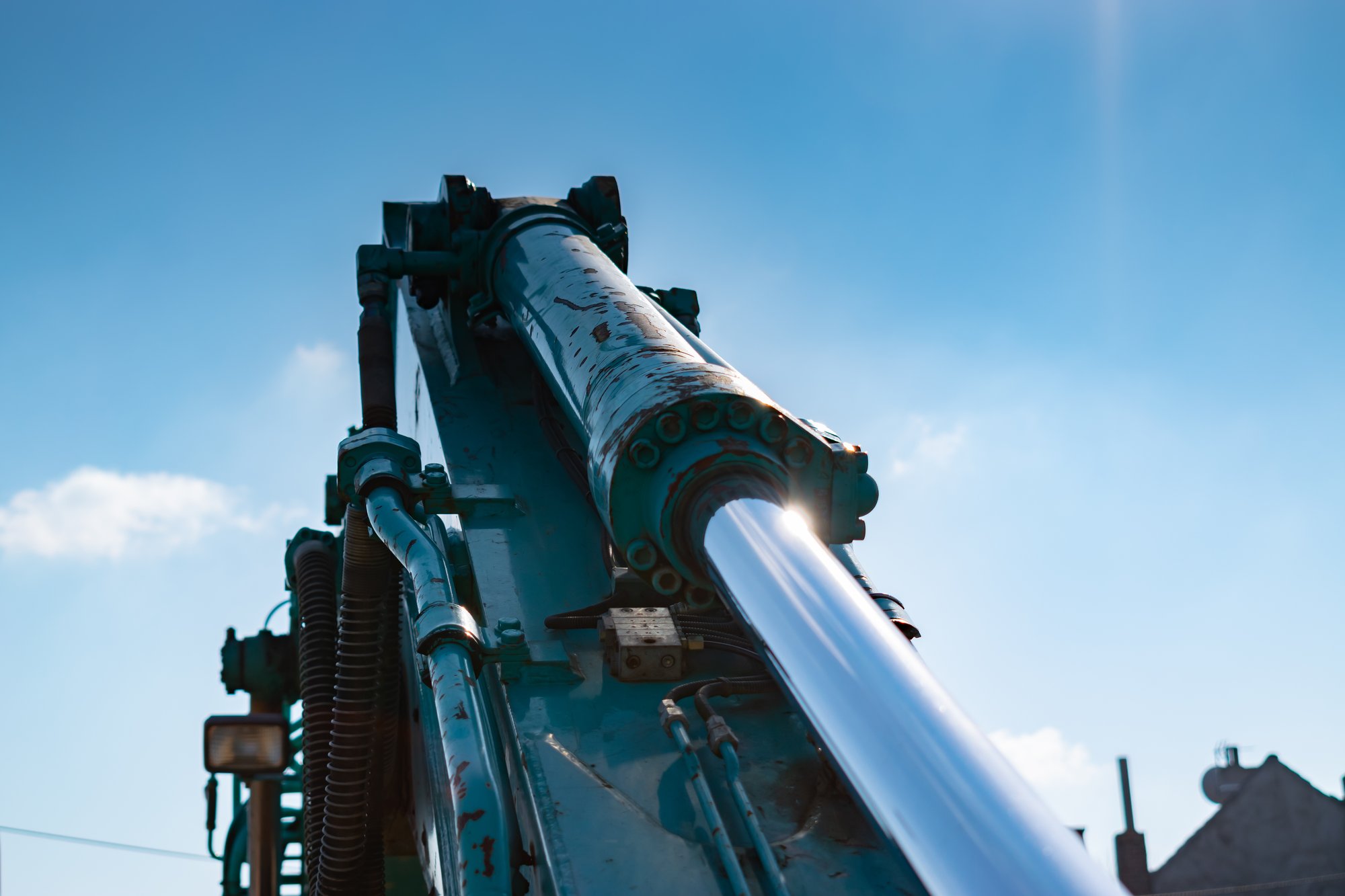
Hydraulic Cylinder Resources
To help understand aluminum hydraulic cylinders as deeply as you would like, we have created and compiled useful resources, including:
Frequently Asked Questions
Have Question? We are here to help
What are the advantages of aluminum hydraulic cylinders compared to steel?
Aluminum cylinders are lighter, which makes them ideal for applications where weight is a concern. They are also resistant to corrosion, particularly in environments exposed to moisture or chemicals. However, steel cylinders are generally stronger and better suited for high-pressure applications.
Are aluminum hydraulic cylinders suitable for high-pressure applications?
Aluminum cylinders are typically used in low- to medium-pressure applications. For high-pressure environments, steel or other materials may be more appropriate due to aluminum’s lower strength-to-weight ratio compared to steel.
What industries commonly use aluminum hydraulic cylinders?
Aluminum hydraulic cylinders are commonly used in industries where weight and corrosion resistance are key, such as in aerospace, automotive, food processing, marine, and material handling industries.
What maintenance is required for aluminum hydraulic cylinders?
Regular inspections are needed to check for leaks, wear, and contamination of hydraulic fluid. Ensure seals are intact and free from dirt. Lubrication of moving parts, where applicable, and periodic fluid replacement are essential for long-lasting performance.
Are aluminum hydraulic cylinders more expensive than steel ones?
Aluminum cylinders may be more expensive initially due to material and manufacturing costs, but they can offer long-term savings resulting from lower transportation costs (due to lighter weight), reduced energy consumption, and lower corrosion-related maintenance.
Can aluminum cylinders handle harsh environmental conditions?
Yes, aluminum cylinders are highly resistant to corrosion, making them well-suited for harsh environments, including those with high humidity, salt air (marine), and chemical exposure.
What are the weight limits of aluminum hydraulic cylinders?
The weight limit for aluminum hydraulic cylinders varies by design and manufacturer. Generally, aluminum cylinders are best suited for applications that do not require extreme force. In contrast, teel cylinders are more robust for heavy-duty work.
Can aluminum hydraulic cylinders be customized?
Yes, many manufacturers offer customization options, such as specific bore sizes, stroke lengths, mounting configurations, and seal materials to meet the needs of different applications.
How do I choose the right seal material for my aluminum hydraulic cylinder?
The seal material should match the operating conditions. For example, polyurethane seals work well in standard conditions, while high-performance fluoroelastomers are better for high temperatures or chemical exposure.
What is the typical lifespan of an aluminum hydraulic cylinder?
The lifespan depends on application, maintenance, and environmental conditions. In general, with proper care and maintenance, an aluminum cylinder can last many years. Frequent exposure to corrosive environments or extreme temperatures might reduce its life expectancy.
What is the maximum temperature aluminum hydraulic cylinders can withstand?
Aluminum cylinders typically handle temperatures up to 200°F (93°C). For higher temperatures, special seals and coatings may be required to prevent damage and maintain functionality.
How does aluminum's corrosion resistance compare to stainless steel?
Aluminum has good corrosion resistance, especially when anodized. However, stainless steel generally offers superior corrosion resistance, especially in highly corrosive environments like those with chlorides or acids.
What are the lead times for ordering custom aluminum hydraulic cylinders?
Lead times depend on the complexity of customization and the manufacturer’s capacity. Standard aluminum cylinders might take a few weeks while custom designs could take 6-8 weeks or more.
Can I replace steel hydraulic cylinders with aluminum ones?
Yes, but only if the application does not require the higher pressure-handling capacity and strength of steel. Aluminum may be a good replacement for lighter-duty applications where weight reduction or corrosion resistance is a priority.
How do I know what size cylinder to choose?
The right cylinder size depends on the force required, the operating pressure, and the stroke length. Our engineers can help you calculate the needed cylinder size based on your application requirements.
Contact Us
To learn more about how our innovative hydraulic cylinders are made with premium coatings and materials can deliver outstanding performance in highly corrosive environments, provide longer cylinders life, and decrease your maintenance costs, tell us who you are and briefly describe your application.
When you use HDM’s field-proven cylinders, you’re getting products and systems that are reliable, rugged and high-performance.
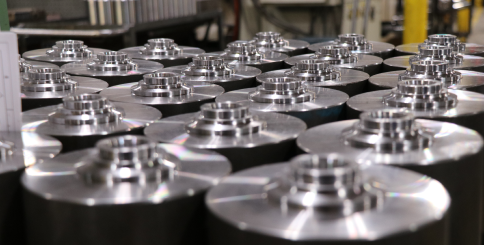